NX Series Features
Robust and Reliable 5 point twin-toggle mechanism
Rugged clamp mechanism
Low platen deflection and better mould life
Highly energy efficient advanced Servo/VDP system
Better injection performance
Sub-flighted Screw for better melt homogeneity
Advance control system
Statistical process contol
Highly effcient plate type oil cooler
Quick reponse
Lower dry cycle time
Low noise and vibration
Larger daylight and longer opening storke
Wide and rigid clamping platens to accommodate large size moulds
Unique mould height adjustment
Lesser oil requirement
Features & Options
Injection Unit
Double cylinder balance for injection structure insures the injection base moves in parallel
Four-stage setting for injection speed, pressure and screw speed
Three-stage setting for pressure holding/material charging speed, pressure, and position
Injection position monitoring function
Injection position scale control
Automatic material cleaning function
Three option mode for suck back
Anti skid aluminum patterned cover
The temperature of barrel is controlled by computer PID
Ceramic heating device of barrel
Cooling temperature control system for barrel outlet
The back pressure adjusting function of stored material
Micro adjusting device of nozzle aiming
Screw speed detection
Modular selection of injection units.
Screw speed input in %
Injection speed input in mm/s
Nozzle guard with electrical interlock for operator safety
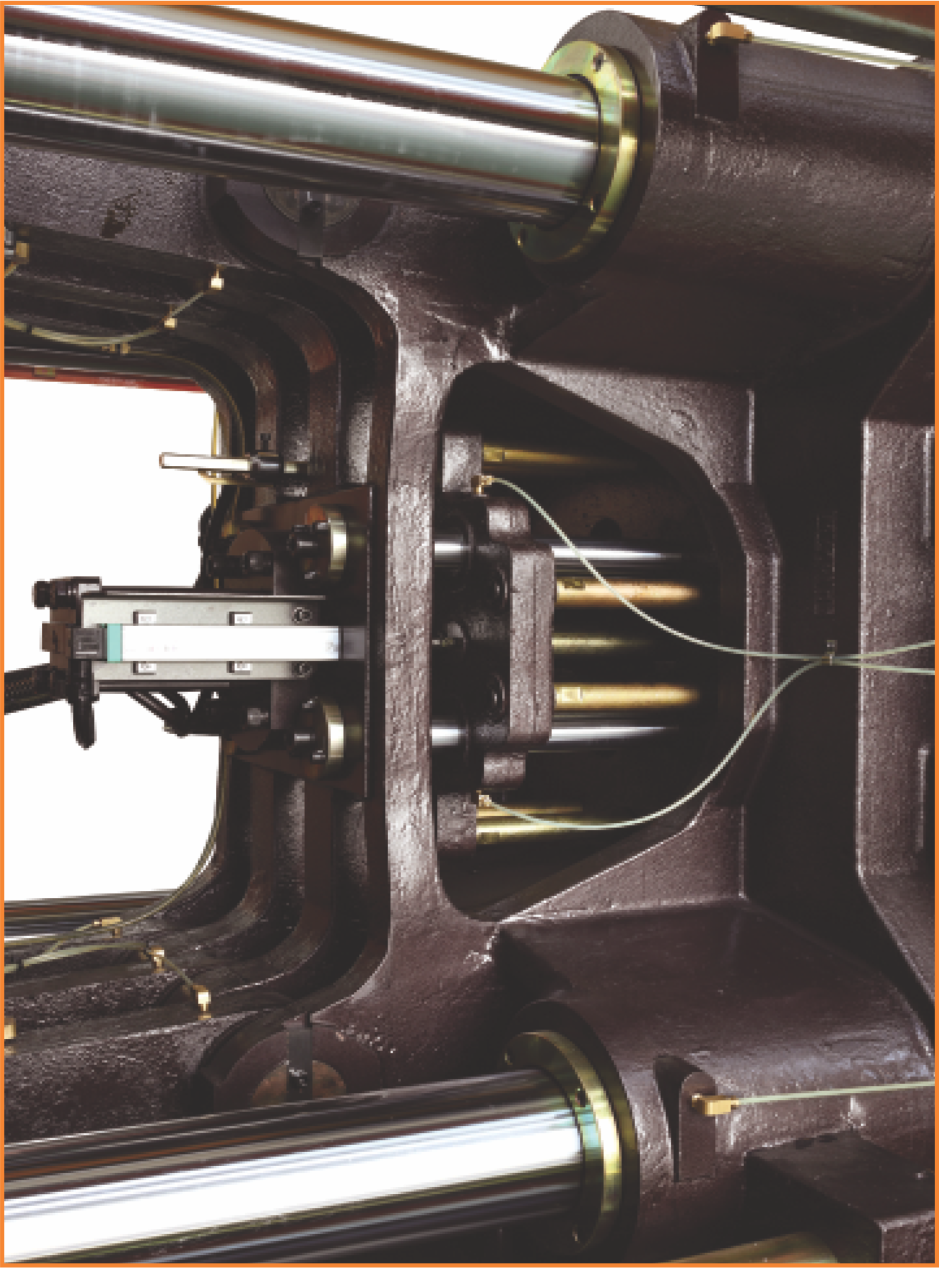
Clamping Unit
Digital four stage control for prreseure , speed, position of mould opening and closing.
water manifold
Automatic centralized lubrication system
High speed mould clamping function.
Special treated tie bar with reliable strength.
Opening/closing mould, ijection position controlled by scale.
Automatic mould adjustment
Computer optimized 5-point twin toggle system, for fast, smooth platen movement and even distribution of clamp force
Toggle bushing grease lubricated automatically : lubrication signals computer optimised under adaptive control
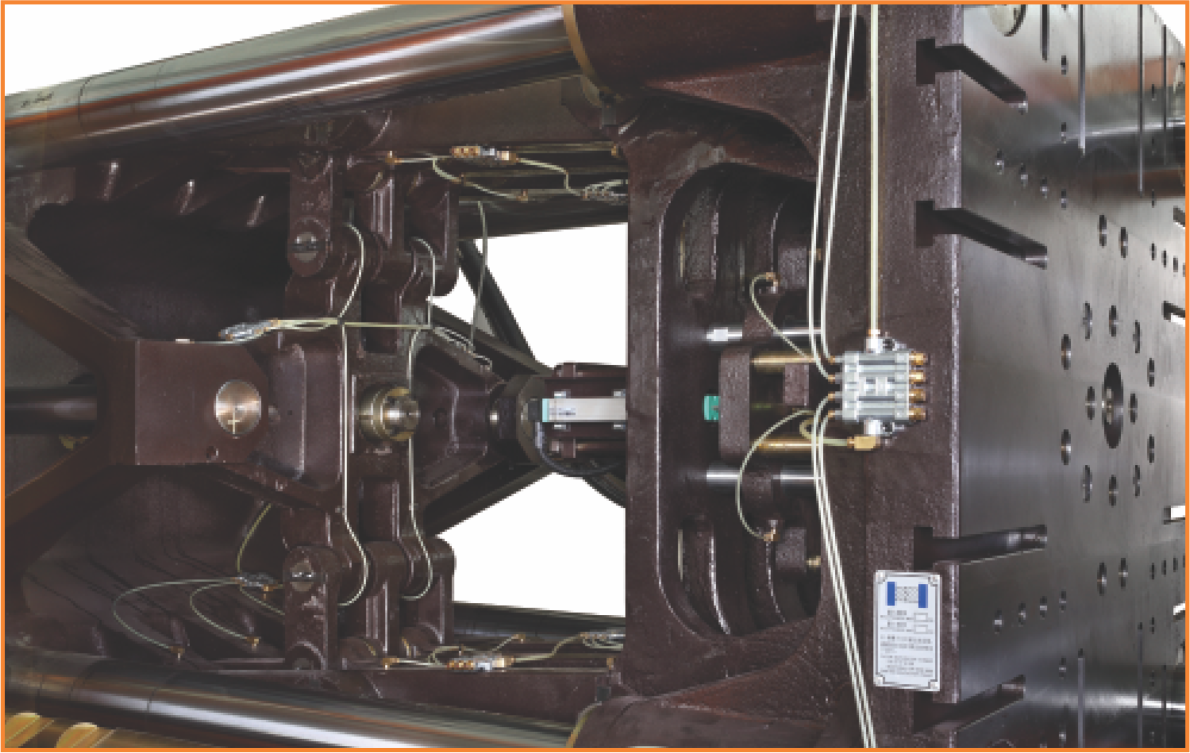
Motorised mould height adjustment through sun & planetry gear mechanism
Low pressure mould safety
Low pressure and slow speed circuit for mould set up
Central hydraulic Ejector with multiple Stroke feature
Pressure and speed Independentally set in both directions
Ejector speed programmable in 2 stage
Central ejector rod
Hydraulic and electrical interlocks for safety gates
Mecganical drop bar for safety
Chrome plated tie bars
Electric Unit
Pre-setting of technical parameters
Electric interface of robot
Protection lock for parameter resource
10 inch Large-scale color LCD screen
The memory of mould in computer can reach 99 groups
Live detection to show running condition of each motion
Abnormal fuctional alarm system
Motor safe protection device
Systematic hardware I/O test fuction
3 Perparatory power pulgs for out supply power
Emergent stop protection function
Electric appliance and hardware inter-ware interlock protection function
Quality monitoring
Down time log
Set of electrical power outlets 3-ph 1*16A, 1Ph 1*10A
Process data statics-graphical display
Processing alarm
Diagnostic function-alarm help menu
LAN port for machine networking
Multi-level password function
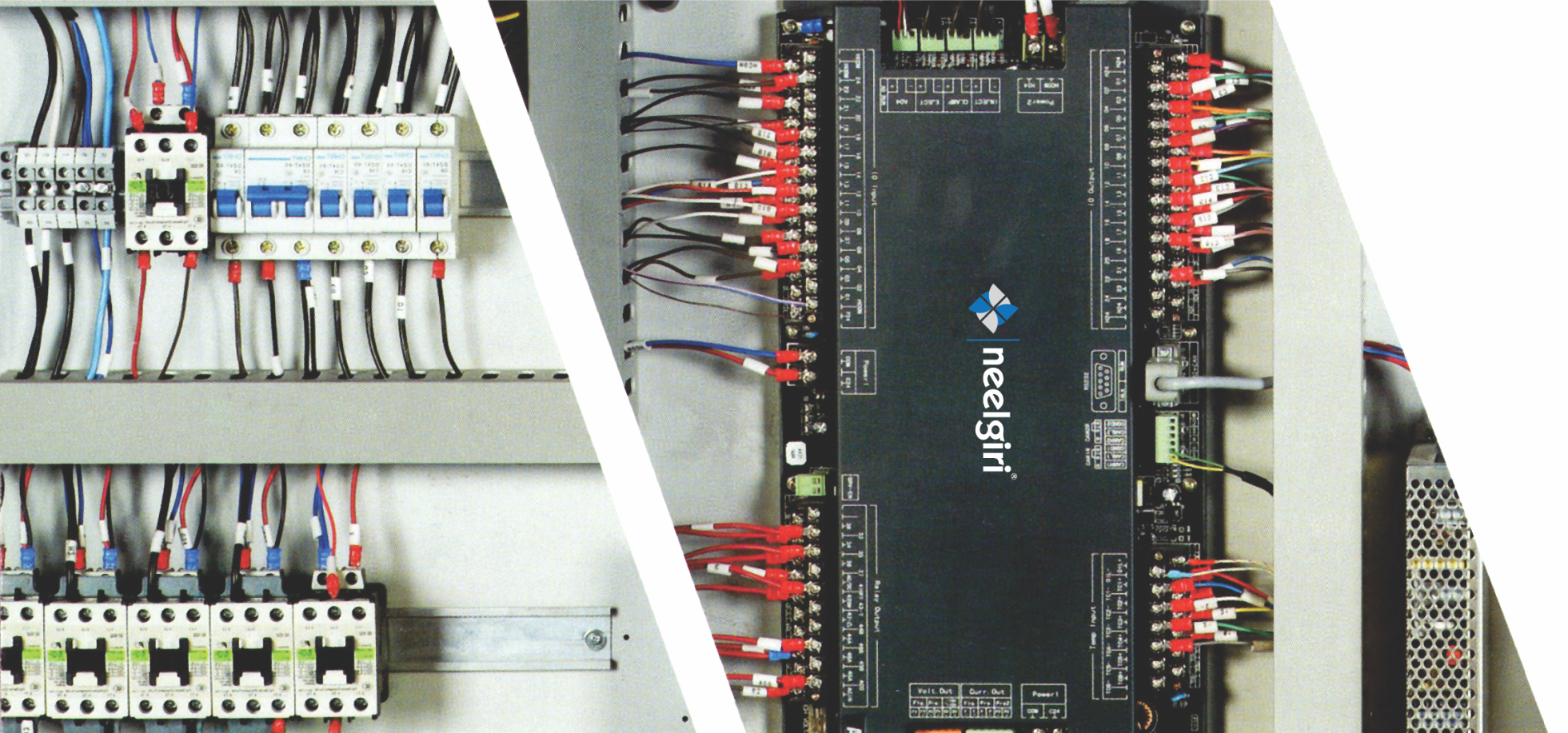
Hydraulic Unit
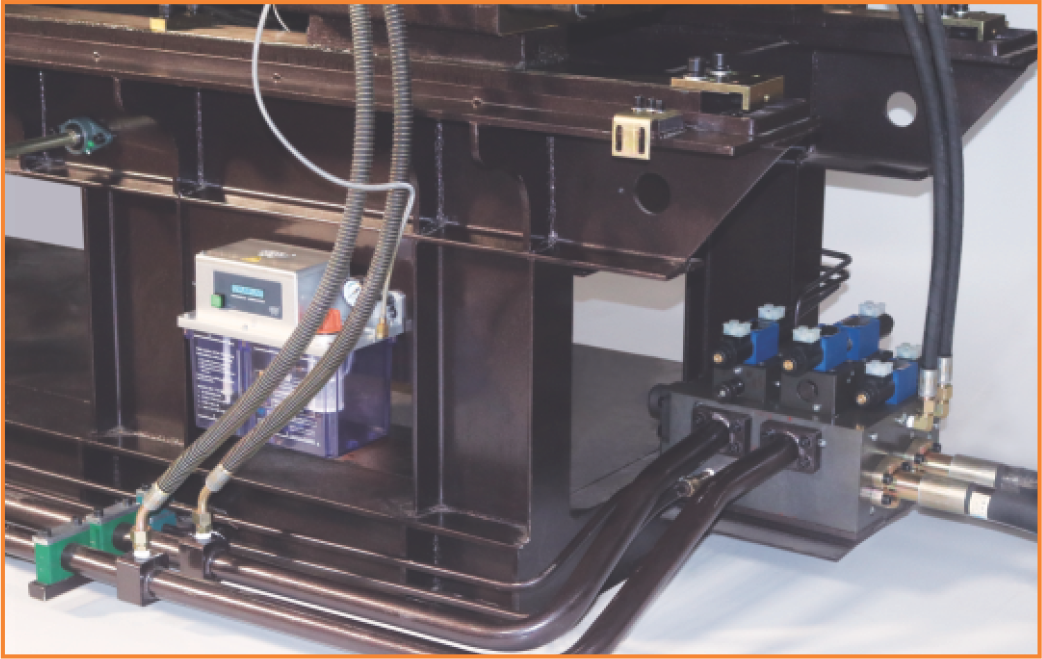
Servo Pump system of high-Performance
Low noise hydraulic control system
Oil temperature deviation alarm system
Oil temperature pre-heating function
Tank oil level indicator
Oil filter core jam alam function
Hydraulic oil cooling device
Self-sealing oil filter of tank
Optional Setting
Special screw for special material
Mould temperature controller
Ejection during mould opening device
Multi-group core-pulling device
Insulation board of platen
Glass tube flow meter
Auto loader
Automatic safe door device
High precision by pass filter system
Proportional back pressure adjusting device
PQ closed-loop control
GSM connectivity for remote monitoring of machine status
Rebot interface as per JIS
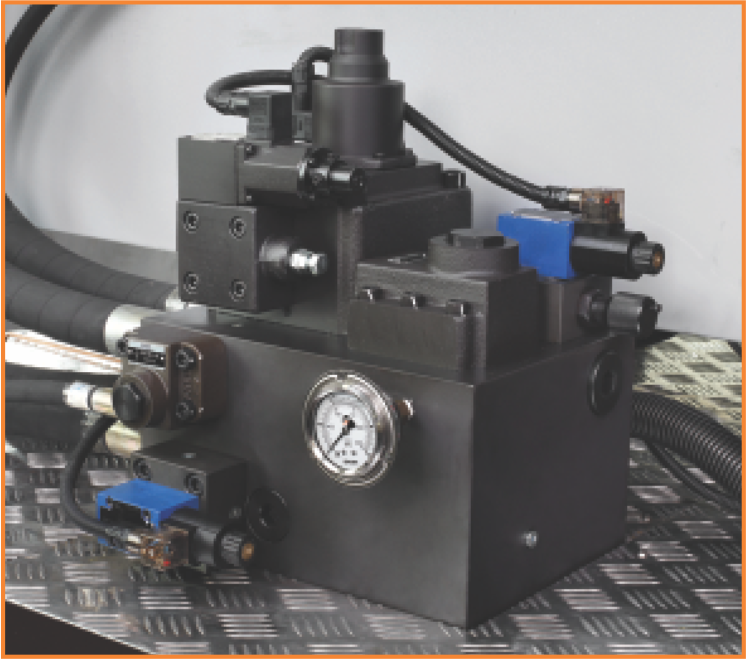